1. Introduction Titanium powder has emerged as a critical material in the aerospace industry due to its unique combination of high strength, low density, excellent corrosion resistance, and superior performance at elevated temperatures. These properties make titanium powder an ideal choice for manufacturing complex and high-performance components that meet the stringent requirements of aerospace applications.
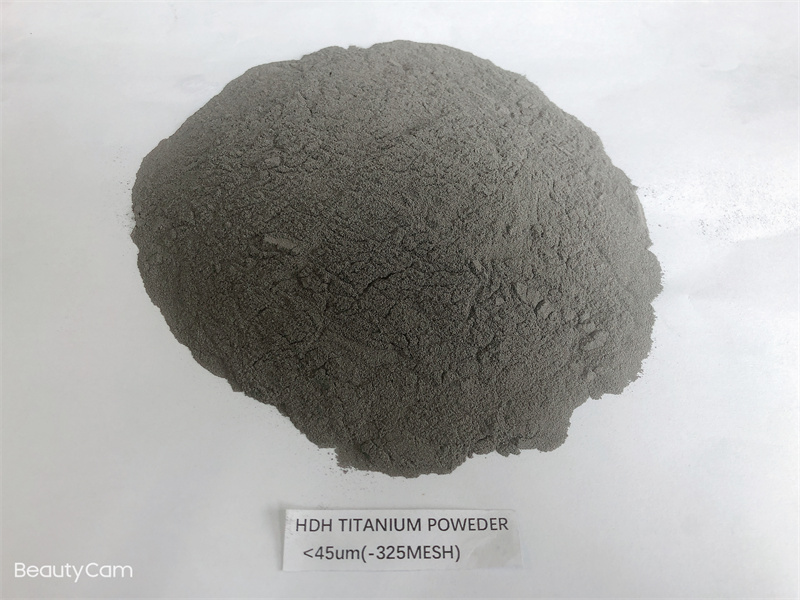
2. Properties of Titanium Powder
Titanium powder offers several key properties that are highly beneficial for aerospace components:
• High Strength-to-Weight Ratio: Titanium alloys, such as Ti-6Al-4V, have a density of approximately 4.42 g/cm³, which is almost half that of steel, making them ideal for weight-sensitive applications.
• Corrosion Resistance: Titanium's superior resistance to corrosion makes it suitable for components exposed to harsh environments, such as seawater and high humidity.
• Temperature Stability: Titanium alloys can withstand high temperatures, making them suitable for aircraft engines and other high-temperature applications.
3. Applications of Titanium Powder in Aerospace
Titanium powder is widely used in the aerospace industry to manufacture various critical components:
• Engine Components: Titanium powder is used to produce compressor disks, blades, and other engine parts. The lightweight nature of titanium alloys helps improve the thrust-to-weight ratio of engines, thereby enhancing fuel efficiency.
• Structural Elements: Titanium powder enables the production of complex internal structures and optimized designs for specific loading conditions. This is particularly valuable for structural components where weight reduction and durability are crucial.
• Additive Manufacturing: Advanced manufacturing techniques such as Laser Powder Bed Fusion (LPBF) and Electron Beam Melting (EBM) utilize titanium powder to create intricate geometries that are impossible or cost-prohibitive with traditional manufacturing methods. These techniques allow for the production of lightweight, high-performance components with reduced material waste.
4. Advantages of Titanium Powder in Aerospace Manufacturing
• Design Flexibility: Additive manufacturing with titanium powder allows for the creation of complex shapes and internal structures that enhance performance and reduce weight.
• Material Efficiency: Traditional manufacturing methods often result in high material waste. In contrast, additive manufacturing using titanium powder significantly reduces waste and lowers the overall cost.
• Improved Mechanical Properties: The ability to control the microstructure of titanium components through precise process parameters leads to enhanced mechanical properties such as tensile strength, fatigue resistance, and corrosion resistance.
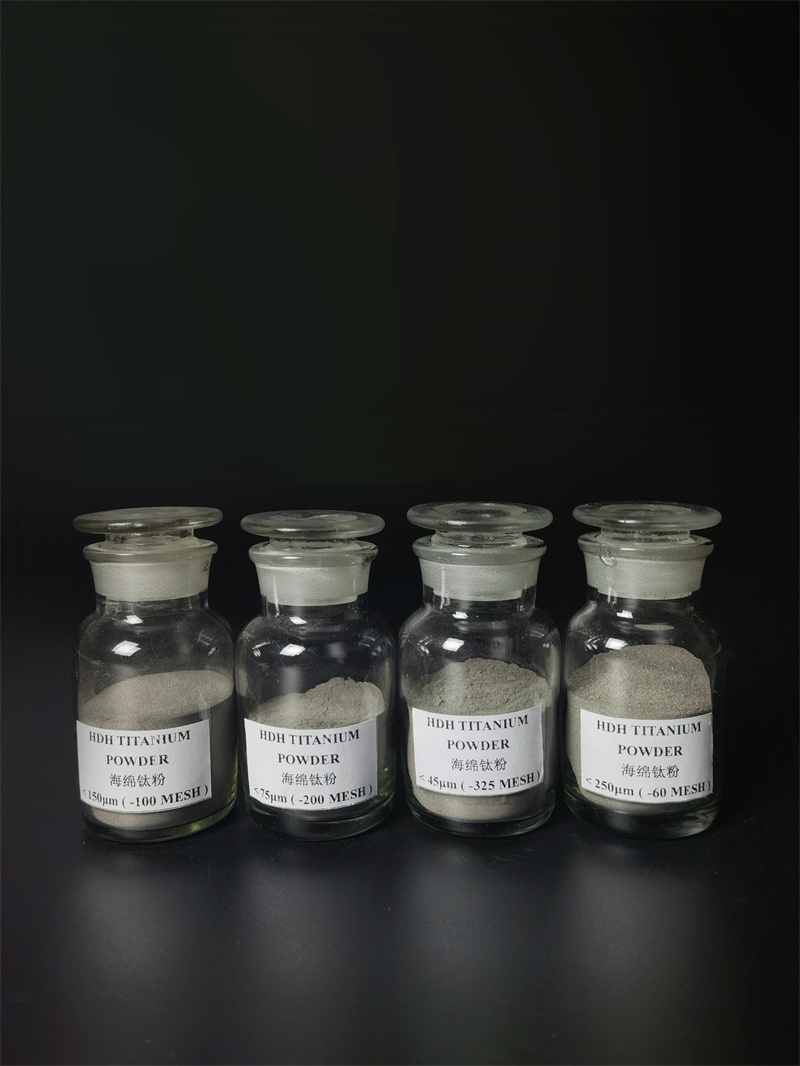
5. Challenges and Future Prospects
Despite its numerous advantages, the use of titanium powder in aerospace applications faces some challenges:
• Process Control: The relationship between process parameters, microstructure, and mechanical properties is complex. Variations in parameters such as laser power, scanning speed, and layer thickness can lead to defects and inconsistent performance.
• Cost: While additive manufacturing reduces material waste, the initial investment in equipment and the cost of titanium powder remain high.
• Qualification and Certification: Ensuring the reliability and consistency of additively manufactured components requires rigorous testing and certification processes.
Future advancements in process control, material science, and cost reduction will further expand the use of titanium powder in aerospace applications. The integration of Industry 4.0 technologies, such as digital twins and automated processes, will enhance the efficiency and quality of titanium components.
6. Conclusion
Titanium powder has revolutionized the aerospace industry by enabling the production of lightweight, high-performance components through advanced manufacturing techniques. Its excellent mechanical properties and design flexibility make it a preferred material for critical aerospace applications. As technology continues to advance, the potential for titanium powder in aerospace manufacturing will only grow, driving further innovation and efficiency in the industry.
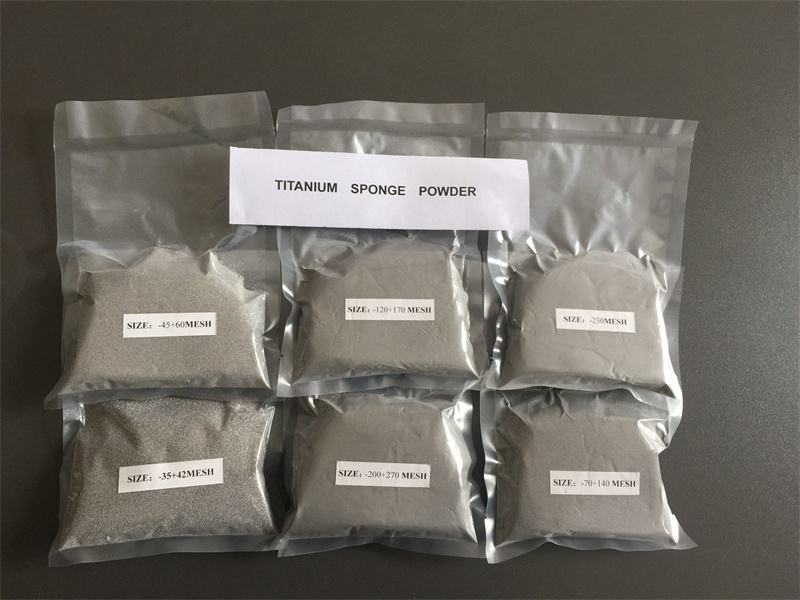
Post time: Feb-28-2025